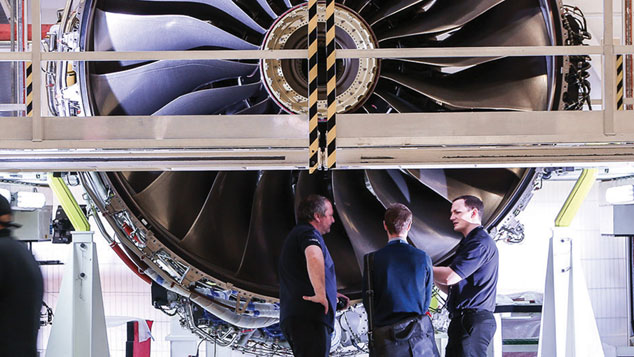
Our metal-bashing industries are not in quite the terrible shape many assume they are, says Simon Wilson. The march of the makers seems to be in full swing.
What’s happened?
British aerospace and defence giant BAE Systems has taken the rare step (for it) of buying a stake in a small, privately held aerospace company, Oxfordshire-based Reaction Engines, which is developing a new kind of rocket engine, called Sabre (“synergetic air-breathing rocket engine”).
Reaction reckons that Sabre could revolutionise global travel, by enabling reusable launchers and space planes to fly at hypersonic speeds of 2,500mph. That would get you from London to Sydney in a little over four hours. BAE has taken a 20% stake in Reaction for £20.6m, while the UK government has given the firm £60m in grants.
How does Sabre work?
The key piece of technology is a “pre-cooler” at the front of the engine, whose purpose is to chill incoming air from 1,000ºC to -150ºC in one-hundredth of a second, as the space plane travels through the atmosphere at five times the speed of sound.
This pre-cooler is made of a special nickel alloy in the form of tens of miles of ultra-thin metal tubing and a cutting-edge frost control system that stops it from freezing up as it flies through humid air. The reason the pre-cooler is so important is that it lets Sabre switch between conventional jet and advanced rocket technologies.
How does it do that?
A conventional jet engine, flying in the Earth’s atmosphere, sucks in air to burn with its liquid hydrogen fuel. But the Sabre’s “pre-cooler” – essentially an advanced heat exchanger – cools the air to a level where it is almost liquid by the time it is ignited.
This means that the Sabre engine can become a conventional rocket engine once the atmosphere becomes too thin above 30km, burning the liquefied oxygen that it carries along with its fuel. This ability to switch modes means that the whole system is also much lighter than conventional rockets, because it doesn’t need to carry oxygen for the launch stage.
What’s the benefit?
In the first instance the revolutionary engine has the potential to slash the cost of satellite launches. In the longer term (a 20-year horizon), Reaction hopes to use the technology to build Sabre-powered passenger jets. But the truth is that at this early stage the range of spin-offs is hard to predict. “I feel like we’re in the same position as the people who were the first to consider putting a propeller on an internal combustion engine,” BAE’s Nigel Whitehead told The Daily Telegraph.
“We understand that there are amazing possibilities, but don’t fully understand what they are, as we just can’t imagine them all. It could be very high-speed flight, low-cost launches to orbit, or other fantastic achievements.” The firm aims to have an engine ready for ground testing by the end of the decade, with flight tests starting in the early 2020s.
Are other breakthroughs waiting?
Perhaps. While many view British manufacturing as being in long-term decline (see below), we have the world’s second-biggest aerospace sector, accounting for 17% of the global market last year (behind only America). This includes big names – such as Rolls-Royce (engines), BAE Systems (fighter jets) and AgustaWestland (helicopters) – but also many other less-heralded companies.
This sector is at the forefront of manufacturing technology. The biggest buzz right now is around “additive manufacturing” – a term that covers a range of processes based on the same principle as 3D printing, which build up components layer by layer from powdered materials.
What’s exciting about this?
“The technology was initially used by the industry to rapidly produce prototype parts”, explains Helen Knight in The Engineer magazine, but it “is increasingly being applied to build in-flight production components for aircraft”.
When the Flying Test Bed A380 aircraft from Airbus takes flight in the coming months, it will mark a “major milestone in aerospace manufacturing”, says Knight. That’s because the Rolls-Royce-made Trent XWB-97 engine powering the aircraft will be equipped with the largest civil aero-engine component ever built using 3D-printing techniques: a front-bearing housing measuring 1.5 metres across, which contains 48 aerofoil-shaped vane components, each of which was produced by 3D printing.
Rolls-Royce isn’t alone in pioneering additive techniques: GKN is using electron-beam melting – where metal powder is melted by an electron beam to build up components layer by layer – in making small- and medium-sized titanium components, such as fittings and brackets. This might not be glamorous, but it is globally sought-after precision engineering of the kind that promises to be the future of UK manufacturing.
How many makers are there?
UK manufacturing output shrank 0.3% in the third quarter, according to statistics published last week. This means the sector remains in a technical recession, battered by a strong pound and fears of a global slowdown linked to the low oil price. This latest tough patch is just the latest episode in a story of apparent decline: manufacturing jobs accounted for around 35% of jobs in the 1960s compared to less than 8% today.
But treat that picture with caution, urges John Cridland of the CBI, the bosses’ union. Cridland reckons manufacturing could account for 19% of the UK economy – almost double the share implied by the national accounts – once you factor in the fact that many manufacturers, including those in the aerospace sector, now develop and sell related services.