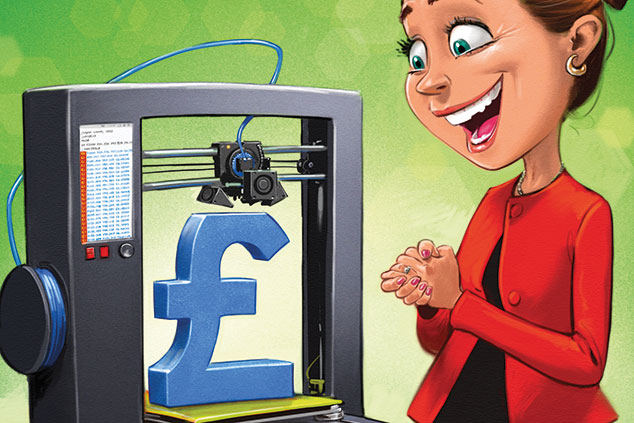
Five years ago, 3D printing was a bubble that burst. But now its time has finally come – and its successor technology, 4D printing, is on the horizon, says Matthew Partridge.
Investing in new technology tends to follow a set pattern. First you have a period where the technology languishes in obscurity. Next you have an explosion of interest, turning into hype. However, when it becomes clear that the technology will take longer than initially expected to develop and go mainstream, there is a collapse in interest – between 2012 and 2014 shares in companies related to 3D printing soared before falling back over the next two years.
Finally, when everyone’s attention is elsewhere, the technology begins to deliver on its promises. The trick, then, is to buy after the bubble has popped and everyone is too traumatised or sceptical to jump back in. Three-dimensional (3D) printing is currently in this position.
Transforming production
The best way to understand 3D printing, and its benefits, is by contrasting it with traditional manufacturing. Until recently, “companies made things in one of two ways: either by carving and shaping blocks of raw materials, or by injecting or pouring liquid materials into a mould”, says Peter Leys, executive chairman of Materialise, which has been involved with 3D printing for nearly three decades. While both processes, particularly moulding, “are very good if you want to produce large numbers of identical objects very quickly at a low cost”, making even minor changes to the objects requires resetting entire production lines and creating new moulds, a time-consuming process.
By contrast, 3D printing is a sophisticated form of manufacturing using specialised equipment, known as 3D printers, to create objects from a digital design by adding together a large number of very small layers of material, some as small as 0.1 millimetres. So an object is essentially created from the bottom up, slice by slice. This means that if you want to change the way something looks, instead of setting and resetting production lines, you can just alter the digital image that is sent to the printer, “drastically cutting the time needed to produce new models”, says Leys.
It can also affect the production process in other ways. For example, “because it is as easy to print 16 variations of a single design as it is to produce 16 copies of one design”, it can make it much easier for firms to focus on producing copies of a product tailored to the individual customer. Objects that can now be 3D-printed range from guitars and guns to medical dummies and engine components.
A big boost to productivity
3D printing also improves productivity by allowing increased complexity. Traditionally complex products had to be split up into several different parts, which were then put together during the assembly process. Because this can be expensive and time-consuming, designers and engineers “are taught… to keep designs as simple as possible in order to make them easier to manufacture”, says Leys, even if this involves compromising on other aspects, such as quality. However, because the 3D-printing process involves creating entire objects in one go, designers can now concentrate on quality “without having to deal with artificial constraints around complexity”.
Subscribers can read it in the digital edition or app